The RUBIG Group today is made up of four divisions – RUBIG Industrial Furnaces, RUBIG Heat Treatment, RUBIG Die Forge and RUBIG Technology. Many decades of experience in metal working and processing, its own on-site competence centre comprising R&D and a materials laboratory, and a dedicated, dynamic team with a creative and innovative approach, form the basis for RUBIG’s position as technology leaders. With its own sites in Austria, Germany, Slovakia, the USA and China, and customers in more than 42 countries, RUBIG is well established on the international stage. And it all began 75 years ago with one small drop forge...
In 1946, the Franz RUBIG & Söhne Metwallwarenfabrik is started in Wels in Austria, in a building which had been bombed during the Second World War. The founder, Franz Rübig, together with his sons Herbert and Helmut, reconstructs the badly damaged building by hand, and sets up a workshop there. RUBIG makes its mark on the market early on with its first product, the injection needle. But it is only the when the company develops its own linchpin that RUBIG has its big breakthrough. With this type of safety connecter, the emphasis is on bending not breaking – naturally without any loss of safety. This concept proves very popular in the agricultural sector and the construction industry, and so the RUBIG linchpin becomes not just the company’s first patented product, but also the trademark of the fledgling enterprise.
1946 - 1955

Success with their first proprietary products gives RUBIG room for growth. Corresponding levels of investment in state-of-the-art production, extending the plant and expanding the product range follow. The development of the flat link chain signifies another important milestone in the company’s history. The chain is a further development of the Ewart chain devised in the 19th century. By changing the type of steel used and the production processes, RUBIG gives it improved resistance to wear, and makes it harder and tougher. As a result it is also ideally suited to heavy loads.
But, with its very rapid growth, RUBIG faces a challenge which the business will have to face repeatedly in the following years: the problem of space. So further premises in Schulstrasse are acquired.
1956 - 1965

The 60s – a time of upheaval and movement; but also of independence and economic prosperity. For RUBIG, this decade does not, of course, signify revolution on a large scale, but the acquisition of its first hydropower plant does mean a significant step towards greater independence and self-sufficiency – after all, a proper smithy needs its own energy source! This made the production process much more cost-effective and allowed RUBIG to focus on the aspect which would become its hallmark – its high quality standards. These also manifest themselves at the start of the 70s in the slogan ‘Safety through quality’.
But it’s not only the high standards placed on the company itself and the efficient management of the business that are decisive for RUBIG’s ongoing growth. The most important factor for success was and is the team. The people who roll up their sleeves every day, set to work and propel the company forward, with creativity, innovative spirit and drive. They are the foundation and the catalysts in any successful business story.
1966 - 1975

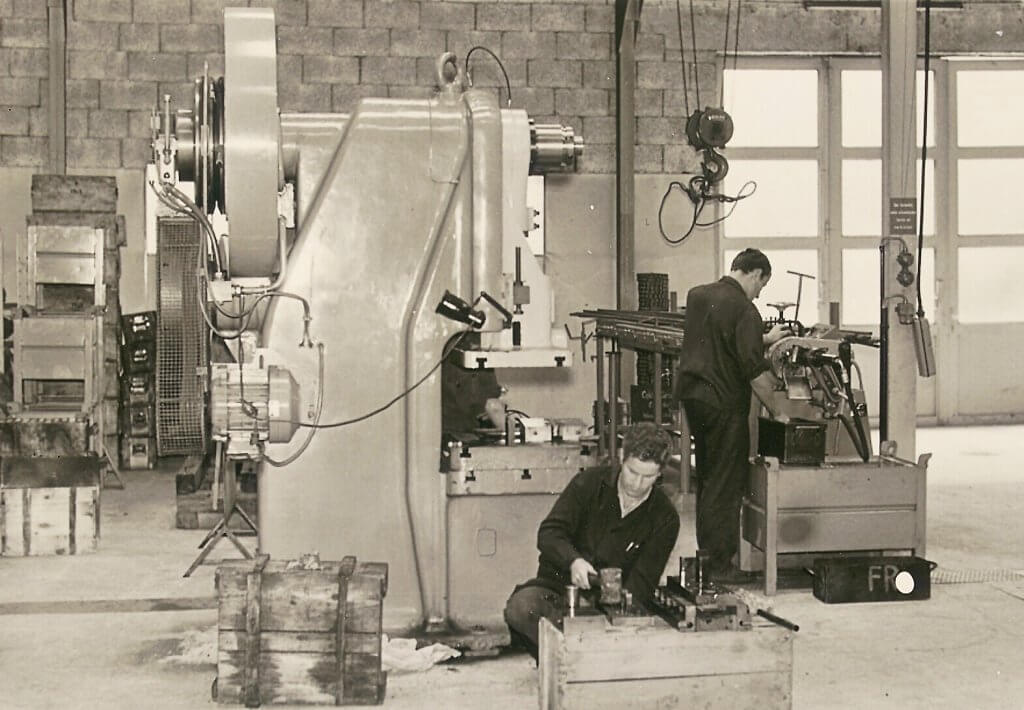
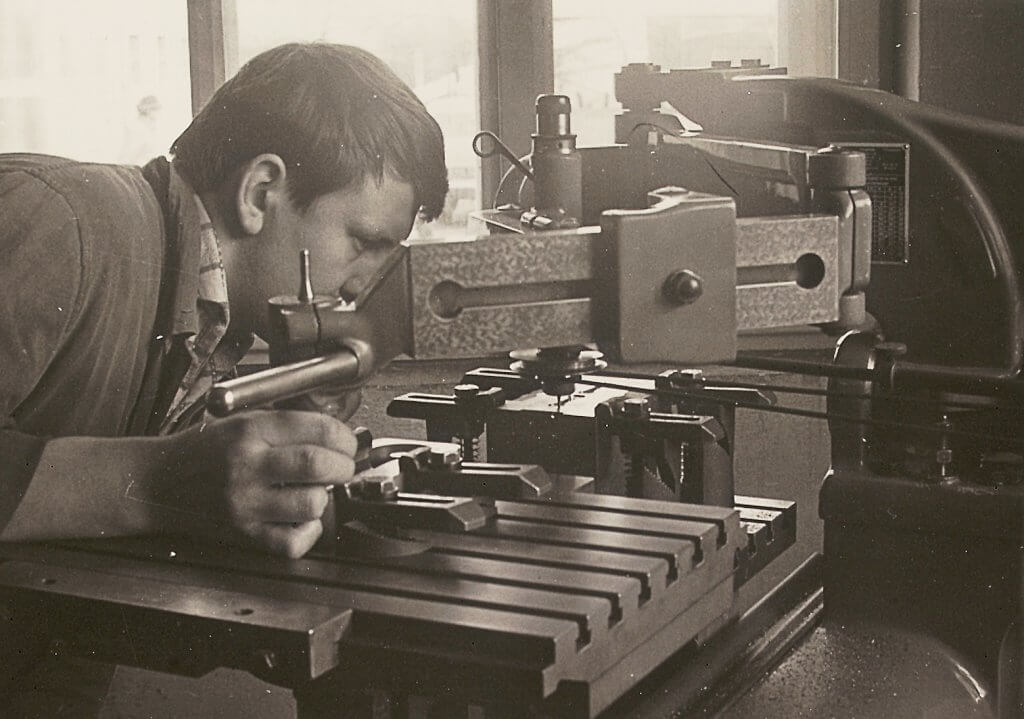
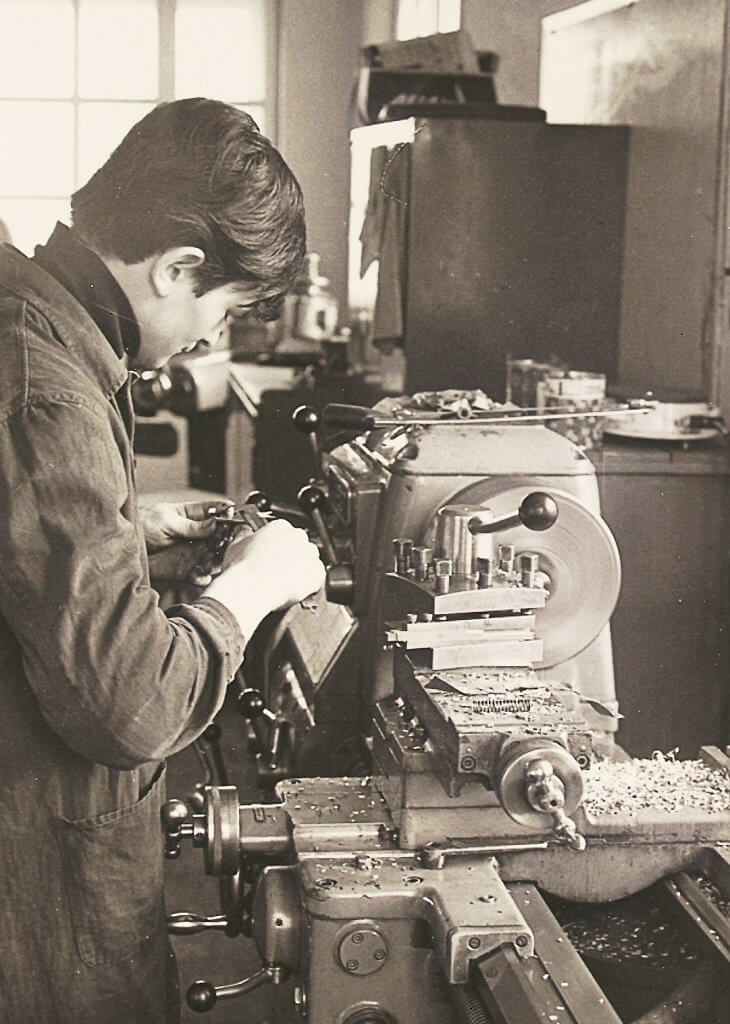
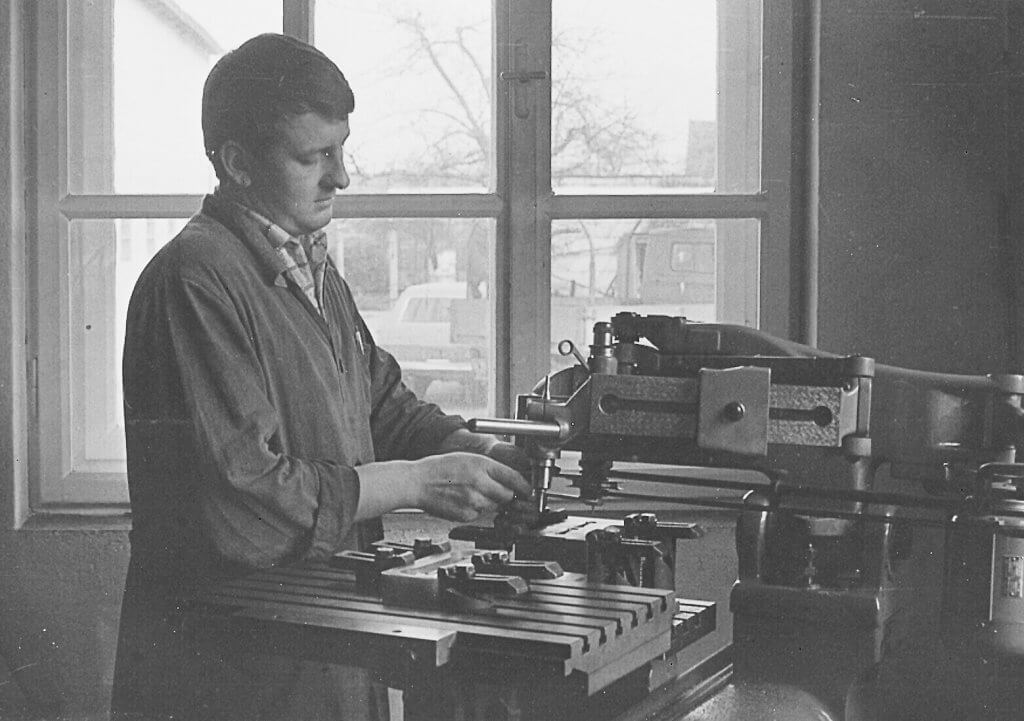
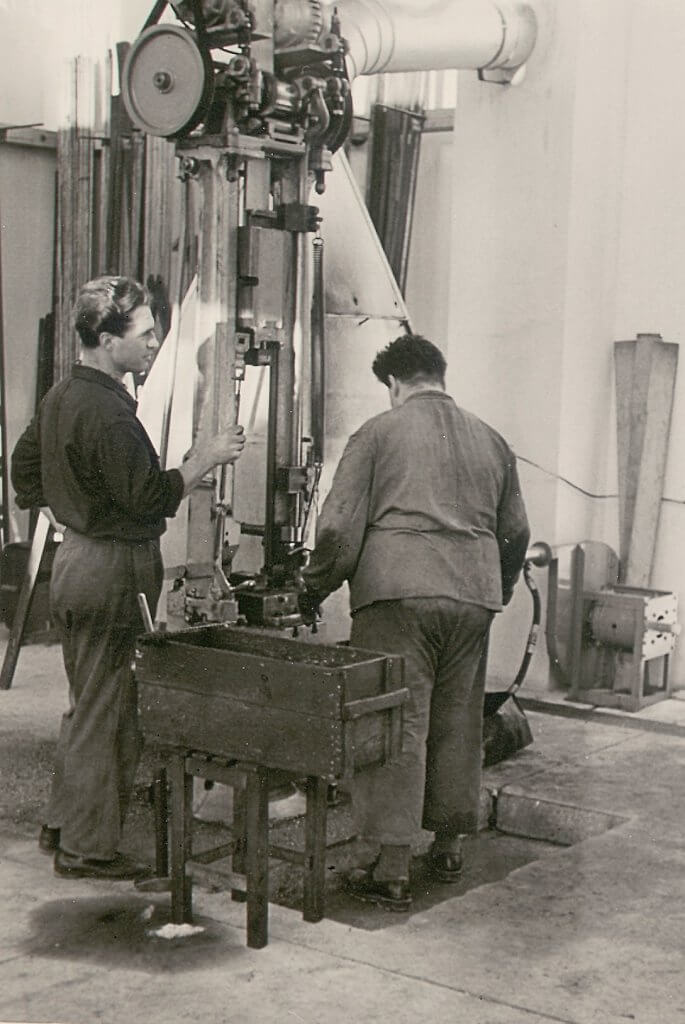
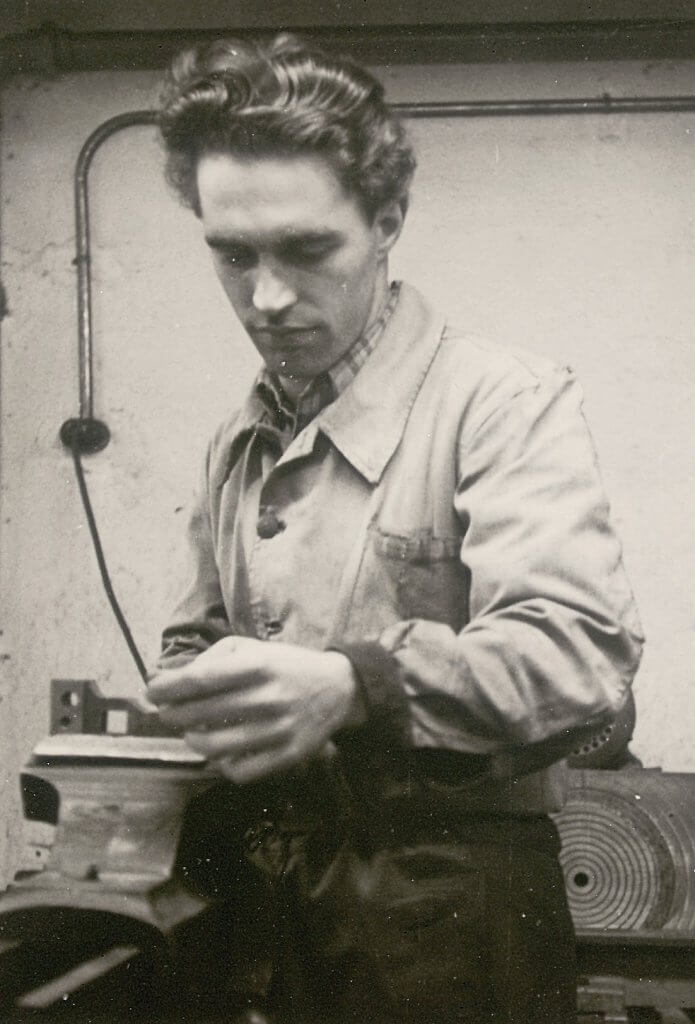
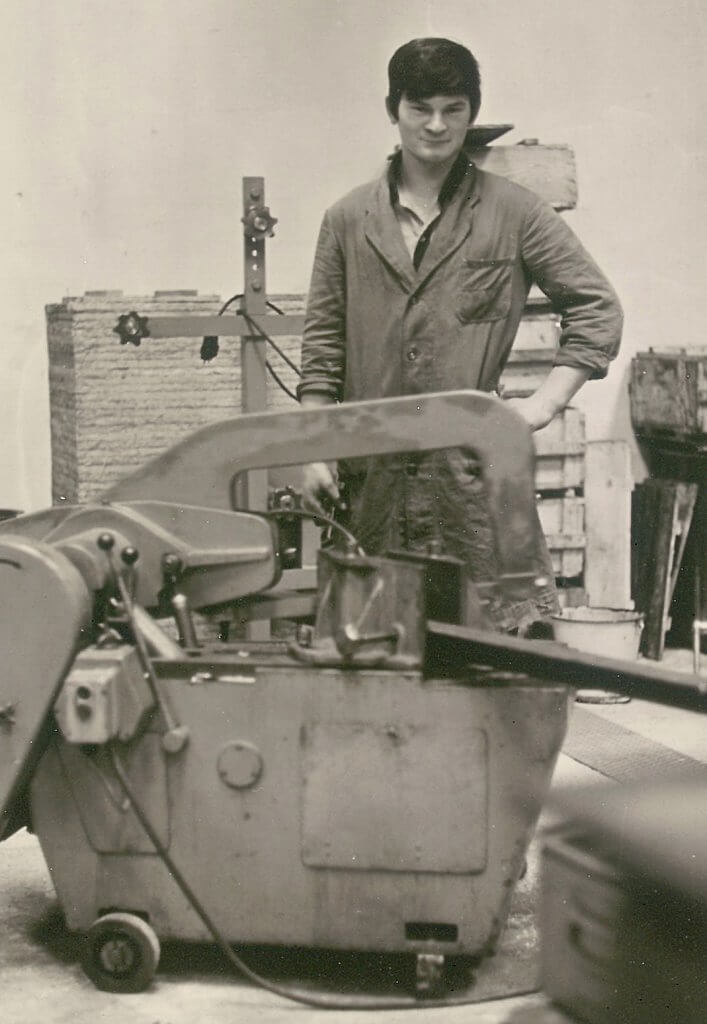
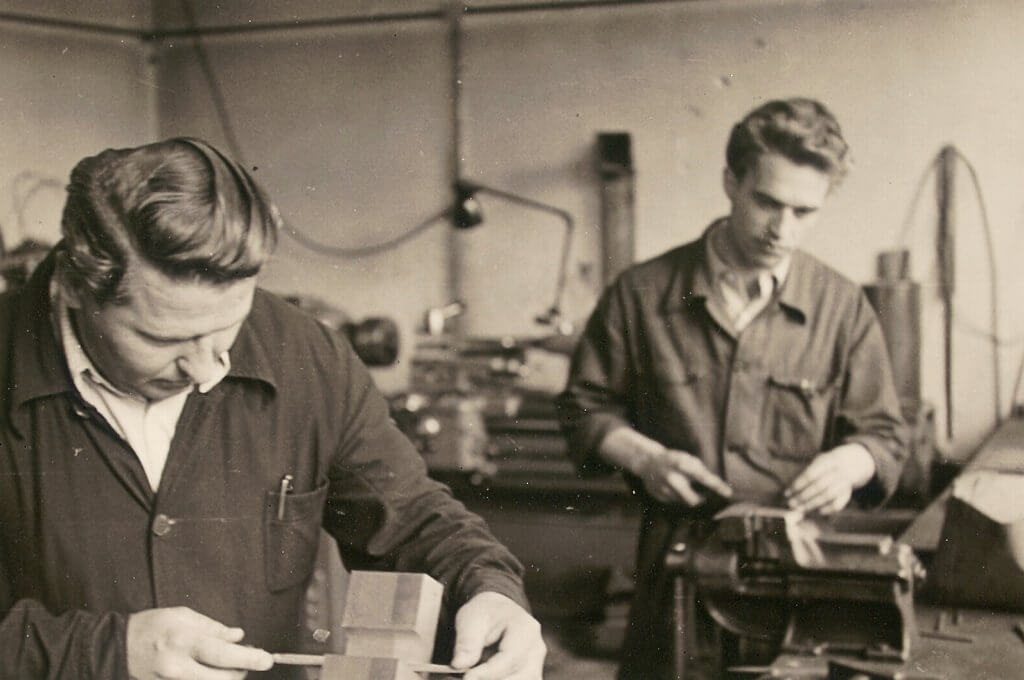
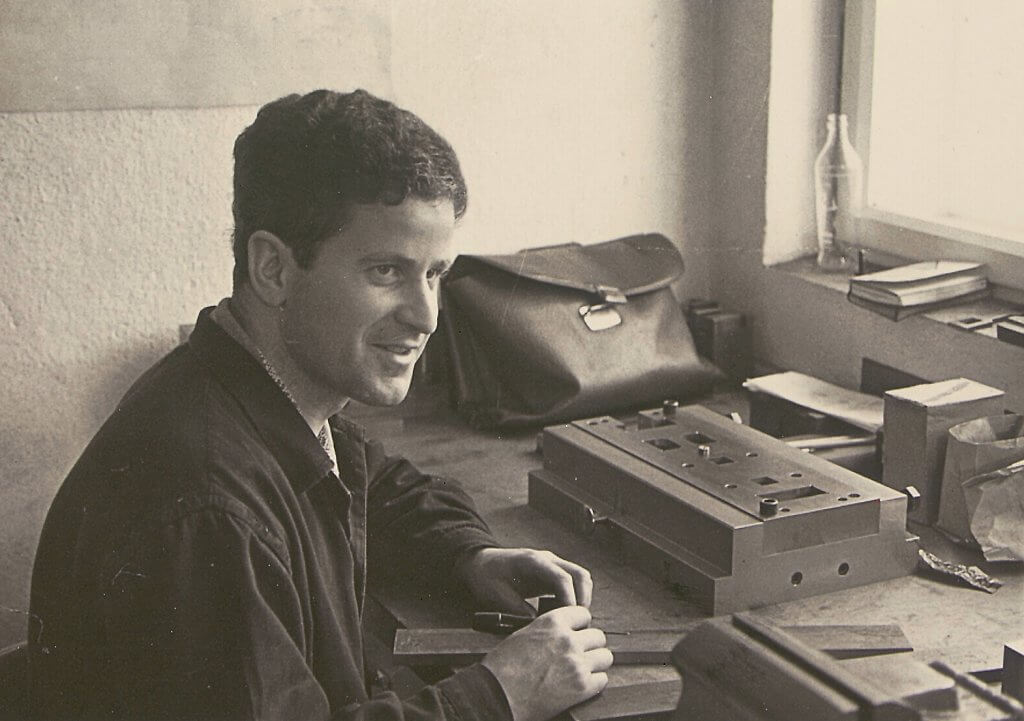
‘The team spirit at RUBIG is unique. Since it was founded in 1946, we have always enjoyed long years of service from our employees, sometimes of 35 years or more, and we often have whole family clans working in the company. This, for me, is the best confirmation that as a business we have done something right. No survey feedback is more effective than recommending your employer to your family and friends.’
At the end of the 1970s and the beginning of the 1980s, RUBIG set a course for expansion – in every area:
expansion in the value chain – the idea for an in-house commercial heat treatment plant is born.
With the acquisition of a second generating plant in Schafwiesenstrasse, clean and secure energy is also guaranteed for the new branch of the company.
Expansion along international borders – the RUBIG safety linchpin wins new customers worldwide.
In order to meet demand, the first international branch office is established in Freilassing in Germany. One after the other, the first agencies in France and England open. The patent for the linchpin, the first in the company’s history, now becomes the first global patent.
1976 - 1985

The official founding of RUBIG Heat Treatment in 1986 – at that time the first commercial vacuum heat-treatment plant in Upper Austria – marks the company’s first step towards becoming a comprehensive centre of competence for metal working. The in-house materials engineering laboratory makes RUBIG stand out from the other commercial heat-treatment centres and gives it a significant competitive edge. Helmut Rübig dedicates himself to achieving this milestone, along with his sons, Günter and Paul Rübig. Early on they recognise the huge potential for synergy held by the new site in Schafwiesenstrasse. In addition to forging tools and products, the components can, after production, also be heat-treated on site.
And it is this that first awakens the entrepreneurial spirit in the three men. The heat treatment technology has scarcely been established before their thoughts start to turn towards the next step in expansion – their own furnace manufacturing plant. It is not long before this idea is realised: in 1992 the opening of a further site in Durisolstrasse in Wels is celebrated. Investment in technological expertise secures the long-term growth of the heat treatment and industrial furnace areas – because here, too, the synergistic effects can be fully exploited. Even today, the plasma nitriding technology developed in-house is an example of a significant driving force for both branches of the business.
1986 - 1995

By the turn of the millennium, RUBIG is bursting at the seams in all directions. By 1997 the global success of the MICROPULS® plasma nitriding technology requires the expansion of the production facility for industrial furnace manufacturing. Shortly after this, the Die Forge division is extended with the addition of a production hall in Mitterhoferstrasse; only the toolmaking shop remains in the premises on Schulstrasse. The space freed up there is used to bring the toolmaking shop, temporarily housed in Durisolstrasse, back to Schulstrasse. But the smithy soon outgrows the space in the Mitterhoferstrasse premises. The administration, marketing and dispatch departments find a new home in the building opposite.
The company’s other locations follow the pattern laid by RUBIG Heat Treatment. Expansion is inevitable. In 2001, the entire division moves to Griesmühlstrasse and acquires the most advanced commercial heat treatment plant in Europe at the time. And the Heat Treatment division also moves not just over the town border to Marchtrenk, but also north-east into Slovakia. In 2005 RUBIG Slovakia is founded. The new location is Nováky – the centre of the automotive industry in Slovakia.
1996 - 2005

The expansion course the company is following also progresses rapidly in this decade. In 2006, RUBIG Aluminium GmbH is established at 4 Griesmühlstrasse. With the addition of this important business area, the RUBIG Group extends and rounds out its portfolio as a competence centre for metal working. This strategic step proves successful – by the end of the decade, the new area has already expanded to include a branch in Pilsting in Germany.
RUBIG Heat Treatment, to which the newly established branch is officially assigned, is also set on a growth trajectory. The plasma nitriding and hard coating sectors are proving to be tech markets of the future. MICROPULS® technology becomes a flagship for the company.
Die 2007 gegründete Motortechnik legt den Fokus ihrer Aktivitäten auf die Entwicklung und Fertigung von Hochleistungskartmotoren und Hinterachsen.
Their success and their investment in technological advancement over the previous years help RUBIG survive the economic crisis of 2008. After the downturn, the Group recovers quickly, and in 2011 the Die Forge division takes an important step in the direction of economic upturn with the acquisition of a new forging hammer. This move allows the business unit to ensure longer service lives and an increase in production capacity.
On 30 July 2012, the ground-breaking ceremony for RUBIG’s new heat treatment plant in Prievidza, Slovakia, takes place. With this, RUBIG is the first investor from abroad to open a branch in the extensive industrial park in Prievidza, which covers 30 hectares. Also in 2012, a service branch of RUBIG Industrial Furnaces is established in Rockford, Illinois, in the USA. Both sites are officially opened the following summer. One of the first people employed at the USA site, and the future ‘American face’ of the RUBIG Group, is a colleague who has completed his apprenticeship in industrial furnace installation as a plant fitter, and who has lost his heart on the other side of the pond. Admittedly he had fallen in love with a lady, not the company. But we were very pleased to be able to support the couple in their new-found happiness.
2006 - 2015

RUBIG Industrial Furnaces Taicang is established in 2018, functioning as a sales and service branch which provides customers with a comprehensive, professional service. This move takes RUBIG into its third continent.
With the establishment of RUBIG Technology GmbH, founded in 2020, the building that formerly housed RUBIG Heat Treatment in Schafwiesenstrasse in Wels is completely modernised. The laser, as the central element, offers almost unlimited potential in this area of the business. Technologies and processes such as laser deposition welding, laser hardening, and laser cutting and welding can be further developed and optimised here.
2016 - 2021

The RUBIG Group is now a high-tech supplier in areas including aeronautics, the automotive industry and medical technology. The development and advancement of new ideas are as important a catalyst for RUBIG as they have always been. Thus the Group strives to meet the new challenges in society, with, for example, PVD technology and research into antiviral and antibacterial coatings.
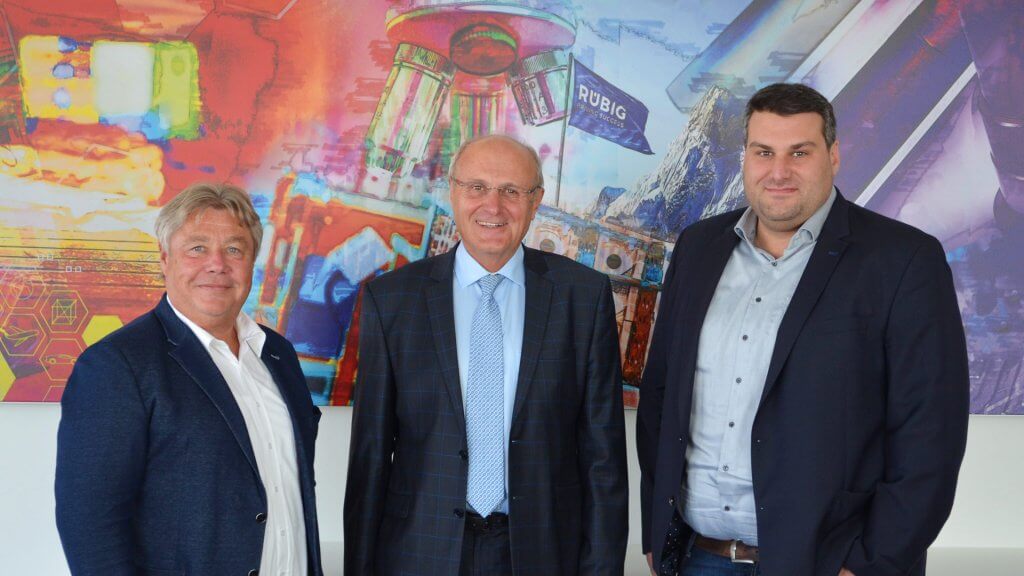